The goal of a manufacturing department is to get the product out the door on time and within specifications. With large batches of products being produced, some sort of quality management system (QMS) is needed to ensure the best and most compliant product is delivered to consumers. A QMS may start out as a paper-based system and slowly transition to a spreadsheet, but without a fully automated and validated system, manufacturers risk security and compliance issues.
So - having a quality management system sounds great, right? It should be a no-brainer to have the QMS validated, right? But you may face a real struggle to get buy-in from decision makers to automate and validate your QMS. Many organizations have trouble finding the bandwidth among qualified staff to perform the initial QMS validation, as well as periodic reviews or revalidations.
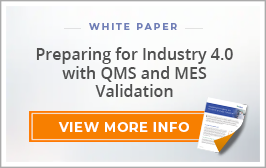
The benefits of an automated and validated QMS include protecting your organization from the consequences of not doing it. No one wants to get an unannounced visit from a regulatory agency and potentially be shut down for violations that a QMS could help you prevent. As the business grows and the demand for system interconnectivity increases, manufacturers won't be able to put off QMS automation and validation.
If you're not convinced yet, we've written this blog to help you understand better why proper QMS validation is important. We begin by sharing some of the benefits of automating the QMS and then 10 reasons why it should be validated in a regulated organization.
The Benefits of Automating Your QMS
The first step in validating the QMS is automating it. The benefits of automating a QMS instead of using a paper-based system are numerous and significant. The following are some of them:
Efficiency: Automation streamlines processes, reducing the time and effort required for various quality management tasks. The tasks of manual data entry, paperwork handling, and physical storage of documents are eliminated.
Accuracy: Automated systems reduce the risk of human error, ensuring that data points are consistently and accurately recorded and reported. This is crucial for maintaining high-quality standards.
Real-time Information: An automated QMS provides real-time access to quality-related data and reports. This allows for immediate decision-making and issue resolution, contributing to improved product or service quality.
Data Integrity: All data sources are secure, and access can be controlled and audited. This ensures the integrity and confidentiality of quality-related information, which is challenging to achieve with a paper-based system.
Visibility and Traceability: An automated QMS offers better visibility into the entire quality process, allowing organizations to track and trace issues or changes from start to finish. This transparency is essential for compliance and continuous improvement.
Compliance: Automated quality management systems often come with built-in compliance features, making it easier to adhere to industry regulations and standards. They can also help organizations stay up to date with changing compliance requirements.
Cost Savings: Over time, automation can lead to significant cost savings. You'll reduce the need for physical storage space, lower printing and paper costs, and minimize the labor required for manual documentation.
Document Control: An automated QMS facilitates document management, revision control, and approval processes. This ensures that the latest approved versions of documents are always available. Outdated or unapproved versions cannot be inadvertently accessed.
Improved Collaboration: Automation allows for better collaboration among teams and departments. Quality-related data and documents can be easily shared, reviewed, and approved by relevant stakeholders.
Performance Analytics: Automated systems can provide in-depth analytics and reporting capabilities. This helps organizations identify trends, areas for improvement, and opportunities for optimization.
Scalability: As your organization grows, an automated QMS can scale with it. It can adapt to new requirements and integrate with other systems and tools more easily than paper-based processes.
Environmental Impact: Going paperless is environmentally friendly, as it reduces paper waste and the associated environmental footprint.
The advantages gained by QMS automation are found not only through efficiency and accuracy but also through promoting a culture of quality, compliance, and continuous improvement within an organization. These benefits can result in enhanced customer satisfaction, reduced risks, and overall business success.
There are many commercial QMS products that can be implemented in your operating environment, and many of your existing systems (such as your manufacturing execution system or enterprise resource planning software) may have a QMS module available at an added cost.
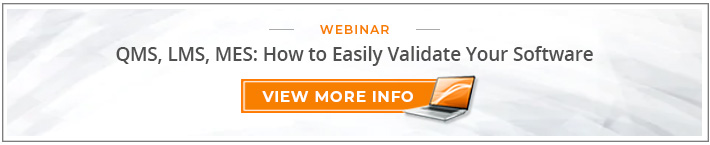
Possible Effects of Not Validating the QMS Software
After the QMS is automated - and can securely maintain training records, standard operating procedures, and deviation reports - it needs to be validated if you are operating in a regulated environment. At CSols, we understand the tension between wanting to adopt best practices and lacking the expertise to fully adopt them. Our qualified validation experts can ensure your QMS (or any other system) is validated, secure, and compliant with applicable regulations. The effects of not validating your QMS can be serious and may result in lost business and other legal and financial penalties. The following is a list of 10 effects of not validating your QMS.
Legal Penalties:
- Civil and criminal penalties: Violations of U.S. Food and Drug Administration (FDA) regulations can result in civil and criminal penalties. Civil penalties can include fines, injunctions, and product recalls, while criminal penalties can lead to imprisonment for individuals involved in noncompliance actions. Validating the QMS ensures that accurate records are maintained and can be accessed in the event of an audit.
- False Claims Act liability: Submitting false or fraudulent information to the FDA can lead to liability under the U.S. Federal Trade Commission (FTC)'s False Claims Act, which can result in significant financial penalties. A validated and correctly applied QMS can ensure that false claims cannot be supported.
Product Recalls:
- If a pharmaceutical, nutraceutical, food and beverage, or tobacco product is found to be in violation of FDA or U.S. Department of Agriculture (USDA) regulations and poses a risk to public health, regulators can require or request a recall of the product. Product recalls can be costly and damaging to a company's reputation. Proper use of a validated QMS ensures that risks to consumers are minimized or eliminated.
Increased Regulatory Scrutiny:
- Noncompliance may result in increased regulatory scrutiny, with more frequent inspections and audits by the FDA or USDA. The accurate recordkeeping supported by a validated QMS can safeguard against noncompliance.
Warning Letters:
- The FDA issues warning letters to companies that are not in compliance with current good manufacturing processes (cGMP) or applicable regulations. These letters identify violations and outline corrective actions required. Failure to address these violations can lead to further enforcement actions. The complete list of FDA warning letters is available on their website.
Injunctions:
- Regulatory authorities may seek court-ordered injunctions to stop the production, distribution, or sale of noncompliant products. Validating your QMS is one way to ensure that the guardrails are in place to keep your products in compliance.
Seizure of Products:
- The FDA or USDA can seize and destroy products that do not meet regulatory standards, especially if they pose a health risk to consumers. The FDA maintains a list of major product seizures on its website. The cost of noncompliance is often orders of magnitude greater than the cost of validating your systems and processes in the beginning.
Consent Decrees:
- In some cases, companies may enter into consent decrees with the FDA, which are court-ordered agreements specifying actions the company must take to achieve compliance. The reliability of data often figures into regulatory decisions and is a factor that can be supported by QMS validation.
Import Restrictions:
- Noncompliant pharmaceuticals may be denied entry into the United States, affecting the ability to market and sell products. A quality assurance issue at a generic cancer treatment drug manufacturer in India is a principal cause of current shortages.
Loss of FDA Approvals:
- Failure to comply with regulations may lead to the withdrawal of FDA approvals or the suspension of licenses for the manufacturing, distribution, or sale of pharmaceutical products.
Damage to Reputation:
- Noncompliance can seriously damage a company's reputation, affecting consumer trust and investor confidence.
▶ Related Reading: Validating Your Enterprise Systems in Life Sciences
A CSols QMS Software Validation Ensures Compliance
QMS validation plays a pivotal role in ensuring compliance with established standards and regulations. It serves as a critical mechanism for verifying that the QMS solution aligns with the specific organizational requirements, industry guidelines, and legal mandates. By rigorously validating the application, businesses can be confident that their QMS functions as intended and reliably produces accurate and compliant results. This not only fosters trust in the quality of products or services delivered but also meets regulatory obligations, thereby enhancing the overall performance and reputation of the organization. If your organization lacks the time or expertise to properly validate your QMS, reach out to us for help.
Comments