You have struggled for a long time with the SAP QM vs. LIMS questions and you have come to the conclusion that SAP QM alone is not a viable solution for your organization to support all the lab processes, workflows, and regulatory needs of your QC lab. You believe that a laboratory data and information management solution would be best to support the lab organization's needs. But the manufacturing operation needs information and data generated in the lab for their SAP QM system that supports the production process.
To support both the lab and manufacturing, you will integrate your lab data and information management system with SAP QM. Whew! Finally done! But are you really done? Read on...
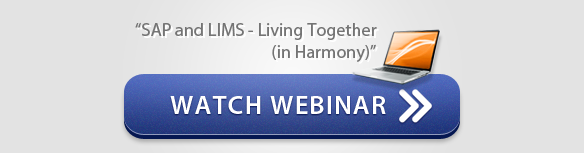
Decisions, Decisions, Decisions
At this point there are still several questions to be addressed in order to implement your chosen approach. The first decision will be which type of lab data and information management system is best for your organization? Should you implement a LIMS, LES, ELN, Instrument Management System, Chromatography Data System (CDS), or a combination of these? The right solution will be dependent on your goals, needs, resources, and infrastructure. Each solution will have its pros and cons, costs and benefits, and challenges.
Luckily, there are several ways to integrate these types of systems to SAP QM. So whatever you decide on for your lab solution, it should support the needs of your manufacturing organization with a little work.
LIMS to Manage the Lab
To simplify things, let's assume that you decide to go with a classical solution which includes LIMS, CDS, and instrument management systems. This will look something like this:
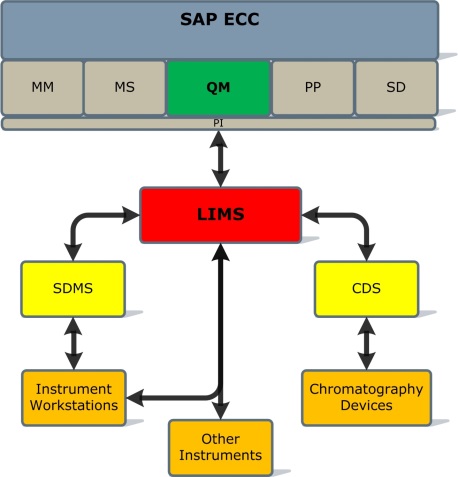
SAP QM / LIMS Integration Basics
First let's take a high level look at how the information flow between SAP QM and LIMS works. SAP QM uses Inspection Lots as the mechanism to notify LIMS that a material needs to be inspected. The inspection data that can be sent to LIMS includes material metadata (e.g., supplier name for raw materials, customer name for finished product, etc.) and material (product) specifications, tests to be performed and results' units of measure. The inspection data also specifies which results (inspection characteristics) need to be sent back to SAP QM.
Now that you understand the basics, you now have another decision to make; one which will be critical to how the integration operates and to your overall success. You will need to decide whether SAP or LIMS will be the master system with regards to material (product) specifications and tests to be performed and which will be the subservient system.
Solution 1: SAP QM as the Master System
If SAP QM is selected as the master, it will be the repository and controller of the material specifications and tests to be performed and will send all this information to the LIMS. The lab will then conduct the testing as specified by SAP, record the data, and send the results back to SAP. One of the big benefits of taking this approach is that the storage and maintenance of your specifications and tests will be centralized and controlled within your SAP solution.
The challenge, however, is that the manufacturing area has now become the owner of this data and any changes or updates, like new test limits for a specification, will have to be made in SAP by the SAP Master Data group who often are resource limited. The LIMS will still support the overall lab operation but the testing will be driven from SAP. In addition it is difficult to fully automate this type of interface when complex analyses are used.
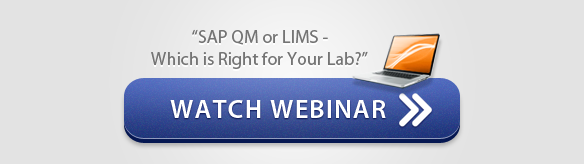
Solution 2: LIMS as the Master System
If the LIMS is selected as the master it will now be the repository and controller of the specifications and tests. SAP will still supply the request for an inspection lot but the LIMS will ensure that the proper testing and limits based upon its specs and tests. The lab will then conduct the testing, record the data, and the final usage decision will flow to SAP through the interface. Because the lab is now the "owner" of the specs and tests, adding or updating entities is usually faster since the LIMS administrator (a lab resource generally) will have higher availability than the SAP Master Data administrators, which is a big benefit.
The biggest issue that can arise in this approach is found in global organizations that have multiple manufacturing sites and multiple LIMS instances. The local LIMS administrators, unless restricted by SOPs, can make changes in the specification and test tables for their instance but the changes will not proliferate to all systems. This can cause the specifications and test definitions to get out of synch across the global organization, which may affect product consistency and overall quality.
Solution 3: Mixed Solution
And, of course, there are a myriad of solutions in between the two extremes, where both systems are responsible for pieces of the inspection data. For example, SAP QM can be the master system for the specifications and LIMS can be the master for the analyses. Care must be taken to ensure that your needs are met by how you elect to implement the integration. Did you implement an integrated informatics solution to support your manufacturing organization? What did you choose for your lab data and information solution? Tell us how you integrated SAP QM and your laboratory data and information management system. Which system was the "Master"?
Comments