Your manufacturing execution system (MES) is a valuable part of your organization's data management plan - if you are using it to its full potential. Is your MES integrated with your laboratory information management system (LIMS) or your enterprise resource planning (ERP) software? If you are operating in the life sciences industry, has your MES been utilized to its full potential? If you haven't thought about your MES as a vital part of your broader organization, you're not alone. However, you shouldn't overlook the potential efficiency gains by leveraging an integrated and validated MES. In this blog post, we'll share why you should consider bringing your MES more fully into your informatics strategy. But first, a little history.
Origins of the MES
Computer technology integrated with mechanical engineering has a long history of increasing production efficiency. The Programmable Logic Controller (PLC) was the first computerized innovation to arrive on the manufacturing line, in 1968. The PLC enabled the deployment of complex logic in manufacturing processes, because programmable control is a natural extension of mechanical engineering. That led to the innovation of computerized control systems such as Human-Machine Interface or Supervisory Control and Data Acquisition (HMI/SCADA), which enabled more efficient management of resources and data gathering to understand failure points and detect faults. Out of these systems grew the first Manufacturing Execution System (MES), in the early 1990s.
The MES and LIMS were recommended as standard practices for the pharmaceutical industry after the United States Food and Drug Administration (FDA) adopted the Code of Federal Regulations 21 CFR Part 11 in 1997. These regulations provided criteria for acceptance by the FDA of the use of these types of systems under certain circumstances, such as for electronic records, electronic signatures, and handwritten signatures executed to electronic records as equivalent to paper records or handwritten signatures on paper.

What an MES Does in the Life Sciences Industry
In the regulated world of pharmaceuticals and biotechnology, many elements of a drug product lifecycle and its ultimate packaging, release, and shipment require validation. Many companies use an MES to interface with LIMS and MRP/ERP systems and track the drug product lifecycle.
- The MES can be the engine that creates a sampling plan and lets users know when samples need to go to the lab for quality testing.
- The MES can print the sample labels, like the LIMS, and the business can get a usage decision (which typically comes from the LIMS) on materials and lots to notify the MES when they are approved for use or rejected.
Getting the most out of your MES and your LIMS in a life sciences business requires an interface between them and then, of course, validation. Consulting an expert in strategic informatics can help you identify what functionality can be hosted in the MES and what must remain in the LIMS or elsewhere. A careful approach to interfacing the MES with the LIMS can spare you a LIMS license for the manufacturing floor, which can be a significant cost savings.
The tricky part of the interfacing is how to first, set up the interface to transfer the data required by the business units; and second, know what should be validated and to what level using a risk-based approach or the new FDA Computer Software Assurance (CSA) draft guidance for critical functionality and events.
▶ Related Reading: Validating Your Enterprise Systems in Life Sciences
Why Does an MES Need Validation
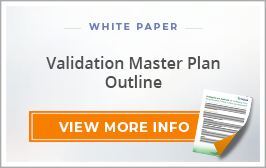
The life sciences MES is a GMP system and therefore subject to validation. Your validation plan is the most important piece of an MES validation because it will help you answer questions like, is the interface going to be one way or bidirectional? What systems will we interface with? Where will the systems and data merge, etc.
MES implementation, integration, and validation can be tricky and costly if not planned and executed correctly. Although some parts of an MES need moderate validation, functions that touch the drug product lifecycle are required to be validated in accordance with current GxP guidance if the organization operates in any regulated space.
Specific situations that require integration and validation which you might encounter include the following:
- Sample generation
- Raw materials (where used) traceability
- Lot kickoff and release to production
- Packaging lots or batches
- Recall analysis
- Kitting for batches
- Electronic batch records
- Batch recipes
Some of these functions can be managed from either the MES or a Product Lifecycle Management tool. Consider batch recipes, for example. These need to be followed exactly. It makes sense to store them in the MES on the manufacturing floor to have the recipe available at the point of use.
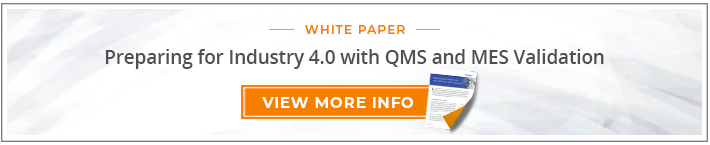
Benefits of Integration Between the LIMS and MES
Many types of informatics software were developed to tackle issues faced by manufacturing plants, such as PLM, Decision Support System (DSS), LIMS, and the very popular Enterprise Resource Planning (ERP) system. These handle issues that arise in industrial settings.
Today, an MES is an essential element of the digital manufacturing technology landscape for the biotechnology and pharmaceutical industries, playing a significant role in digital transformations for organizations in this space.
The integration of an MES to a LIMS has many benefits, which include:
- Digitalization of the plant
- Removal of paper systems
- Increased data integrity
- Real time status in both system
- Regulatory compliance (MES and LIMS validated)
- Increased productivity
It's important to know that some LIMS products interface with an MES or ERP better than others. The underlying code is not always easily compatible.

LIMS to ERP/MES interfacing allows fully digital product processing, including the data associated with that processing. This allows the user community in the Manufacturing Operations Management and Laboratory Operations layers to work together seamlessly, and in real time, with transparency to increase productivity and effectiveness.
Working with informatics solutions providers who not only can navigate the software (MES/LIMS) and IT environments, but also can understand the unique nuances of life sciences manufacturing, is a huge plus. These skills and understanding are critical to success when interfacing and validating an MES for use with informatics systems like a LIMS or an electronic laboratory notebook (ELN).
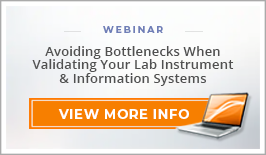
You need a trusted partner to understand the nuances of the manufacturing environment and the pitfalls that can be encountered when working with disparate systems. There are important regulatory compliance benchmarks, as well as the need to understand the As-Is and To-Be workflows. Taking the time to map tout the benchmarks and workflows before doing any interfacing or validation will remove bottlenecks and allow you to not only recast what you already do but also to enhance it. This is where you will really see a return on investment (ROI).
In Summary
Validating the MES and interfacing it with the LIMS, ELN, or ERP allows pharmaceutical and biotechnology companies to gain a competitive advantage with improved quality, better traceability, maximized lean initiatives, flexible manufacturing processes, improved compliance, complete business process management, and accurate real-time reporting.
Companies that do not have a validated MES integrated with their LIMS may lose a share of existing and new market opportunities.
Complementing your LIMS or ELN system with an interfaced and validated MES solution will allow you to see the maximum benefit from each system.
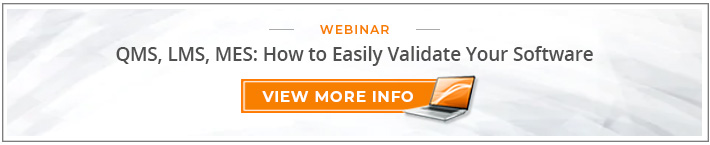
What do you have integrated with your MES? Are all your integrated systems validated?
Comments