If you have ever contemplated installing and implementing a Laboratory Information Management System (LIMS) you will have realized that these solutions can be pricey, both from a capital and resources point of view. It is also likely that you have been requested to justify the investment in the proposed LIMS by developing a Return on Investment (ROI) analysis. In order to accomplish this task, it will be imperative that you understand the full cost of your LIMS solution and the Total Cost of Ownership (TCO) over the return period. Additionally, you will need to determine the cost savings to the lab and organization that the implementation of the LIMS will yield. These quantitative measures are generally the most powerful sources of cost savings and will therefore represent the lion's share of your LIMS cost justification.
There are many sources of cost savings that the automation of lab and business processes and procedures in your LIMS can offer. To find the highest potential cost savings, try exploring the following areas: Reporting, Sample Inventory Location Tracking, Data Results Entry, Calculations, and Review/Approve Results or Samples.
Reporting
There are always a large variety of reports that a lab generates because the main product of a lab is data and information. These can be ad-hoc reports or ones that are run on a regular basis (i.e., daily, weekly, monthly, quarterly, yearly, etc.). There are also reports that are run only when certain conditions arise, such as environmental reports that need to be generated only after a rainfall. Automating the generation and the delivery of these reports to the appropriate parties can be one of the largest sources of cost savings that can be realized when implementing a LIMS.
When analyzing this area for cost savings it is important to understand what role(s) in the organization is actually doing the work (and how much work) to generate, review, edit and finalize these reports. When you translate time savings to cost savings it will be important to break out the time savings by role so you can use the appropriate role based hourly cost to each category.
Sample/Inventory Location Tracking
When you stop to think about it, you will be amazed at the amount of time wasted by your lab personnel trying to find samples, subsamples, equipment, glassware, standards, reagents, and chemicals. Testing can be delayed and a snowball effect may occur when and if critical samples or chemical entities are misplaced. When implementing your LIMS, it is a good general practice to designate locations within the lab, hoods, shelves, stockrooms, freezers, etc. in order to aide in the tracking of samples and other lab entities.
A great tool that will provide even greater cost savings in this space is barcodes. By barcode labeling the locations in the lab's physical infrastructure and barcode labeling the samples/entities to be tracked, you can use your LIMS and a barcode reader to dynamically update the location of your samples/entities. This will enable you to have up-to-date information as to the location of pretty much anything in your lab environment, assuming that your analysts follow your SOPs and use the barcode readers to update the locations as they move samples and other entities through the lab areas.
Data/Results Entry
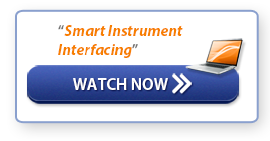
One of the largest sources of cost savings for a laboratory implementing a LIMS can be realized if the organization elects to interface the highest throughput and/or most data intensive instrument systems to their LIMS. Depending on the interface's level of sophistication, which can range from a simple ASCII data dump to a highly complex, two-way programmatic interface with Artificial Intelligence (AI) elements, cost savings can be realized in a number of areas. However, regardless of the sophistication of the interface, one is removing the manual entry of data/results into the LIMS. This, in itself, saves some time for your analysts but it also significantly reduces transcription errors and other human generated errors, thereby saving significant costs associated with the effort needed for reworking of analyses or even the loss of a product batch or stream.
Calculations
Automating, within your LIMS, the processing of calculations is another classic source of cost savings when one is implementing a LIMS. Modern LIMS will support both intra and inter test and sample calculations. The calculation subsystems of different LIMS may well support slightly different functionality but even if an essential mathematical function is not supported, no need to worry. Most LIMS will also support the integration of their system with a more sophisticated calculation/statistics/visualization tool like NW Analytical or SAS.
Remember, not only can you save costs on the time to perform the initial calculation but you also eliminate the time expended by supervisors to rerun calculations by hand to verify them. Since the calculations are automated in the LIMS, there is no opportunity for the introduction of human error, hence no need to rerun the calculations.
Review/Approve Results or Samples
Good Laboratory Practices (GLP) requires that data and results be reviewed and approved by another scientist (i.e. not the person who took and recorded the readings). In a manually run lab operation, these tasks are performed by hand and will take a considerable amount of time to complete manually, but if one implements the LIMS functionality of only requiring the review of results that are outside of the expected limits (i.e., review upon exception), then considerable time and cost savings can be realized. This, of course, is primarily used in a quality control laboratory environment.
The same goes for the review and approval of a complete sample (i.e. not just an individual analysis on the sample). The time and cost savings associated with review by exception can be considerable, however, even larger cost savings can be realized if your organization is running batches of samples along with the associated QC samples (dupes, spikes, repeats, etc.). If this is your scenario, when you perform a sample review, it will be in the context of the QC batch and all the QC samples will need to be reviewed as well. Having all these runs and data available, and integrated with your LIMS, is where significant time and cost savings can be realized.
Do you understand the full cost of your LIMS? Have you determined the potential cost savings that implementation of your LIMS and the automation of your lab and business processes and procedures will drive? Have you explored all the areas listed above for potential cost savings?
Comments